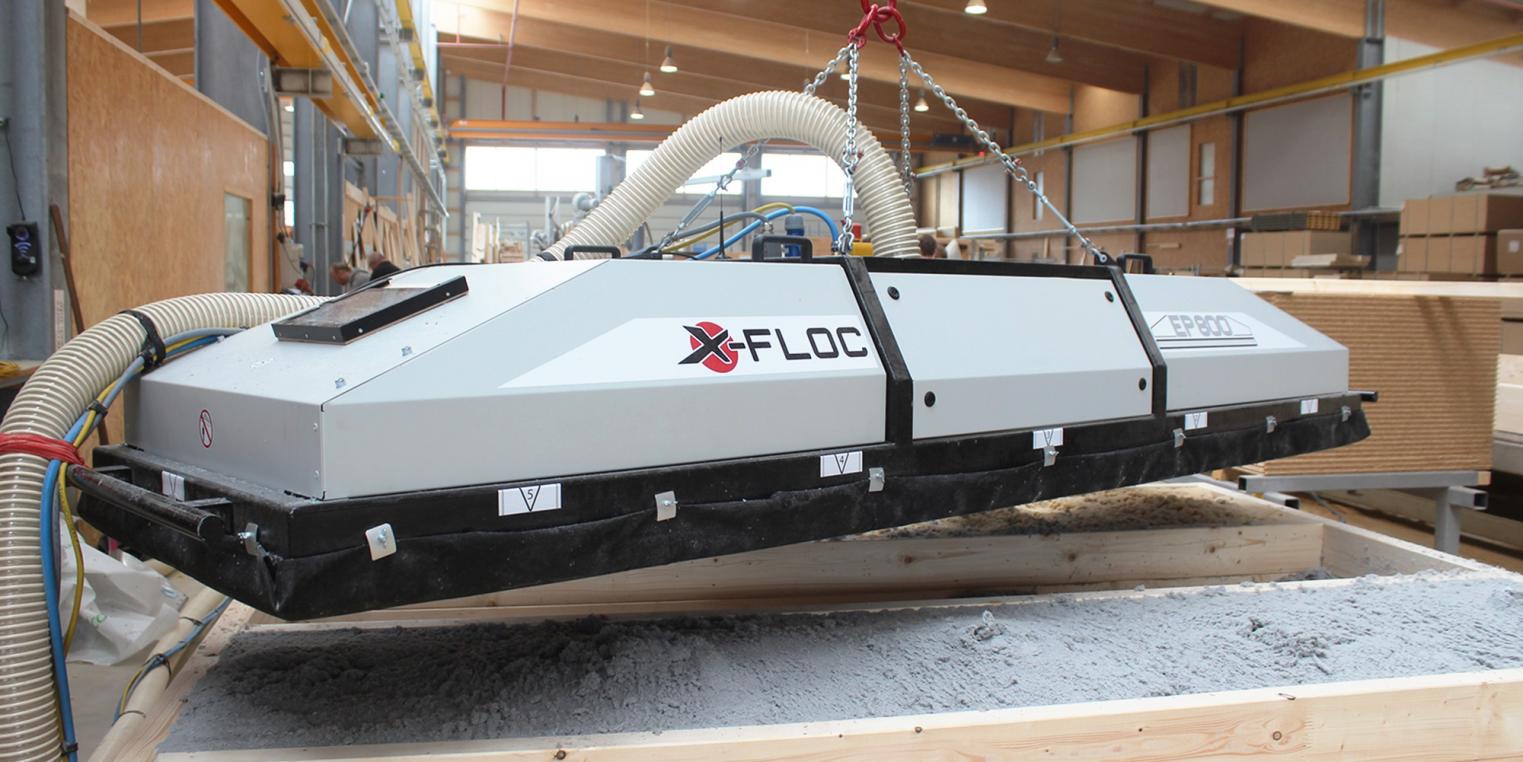
FACTORY INSTALLATION
Factory installation technology for insulating timber frame elements
With the modular x-floc factory filling system, comprising the EP800 blowing panel, GBF1050 big bale conditioner and EM430 blowing machine, combined with the THERMOFLOC big bales, the frame elements virtually insulate themselves.
The high level of automation and consistently high processing quality
optimize staff deployment and give the products industrial quality. The
factory filling system can be adjusted to individual customer requirements and is therefore easily integrated into small companies and fully automated production lines alike.
All advantages of factory filling at a glance:
- Industrial, consistent production processes
- Efficieny due to automation
- Scalable modular plant technology
- Compatibility with different blow-in insulating materials
The industrial factory filling system is designed for refits, new equipment and integration into existing production processes, thus ensuring an optimum production cycle without interruptions. The system is modular and grows with the requirements of the timber construction company.
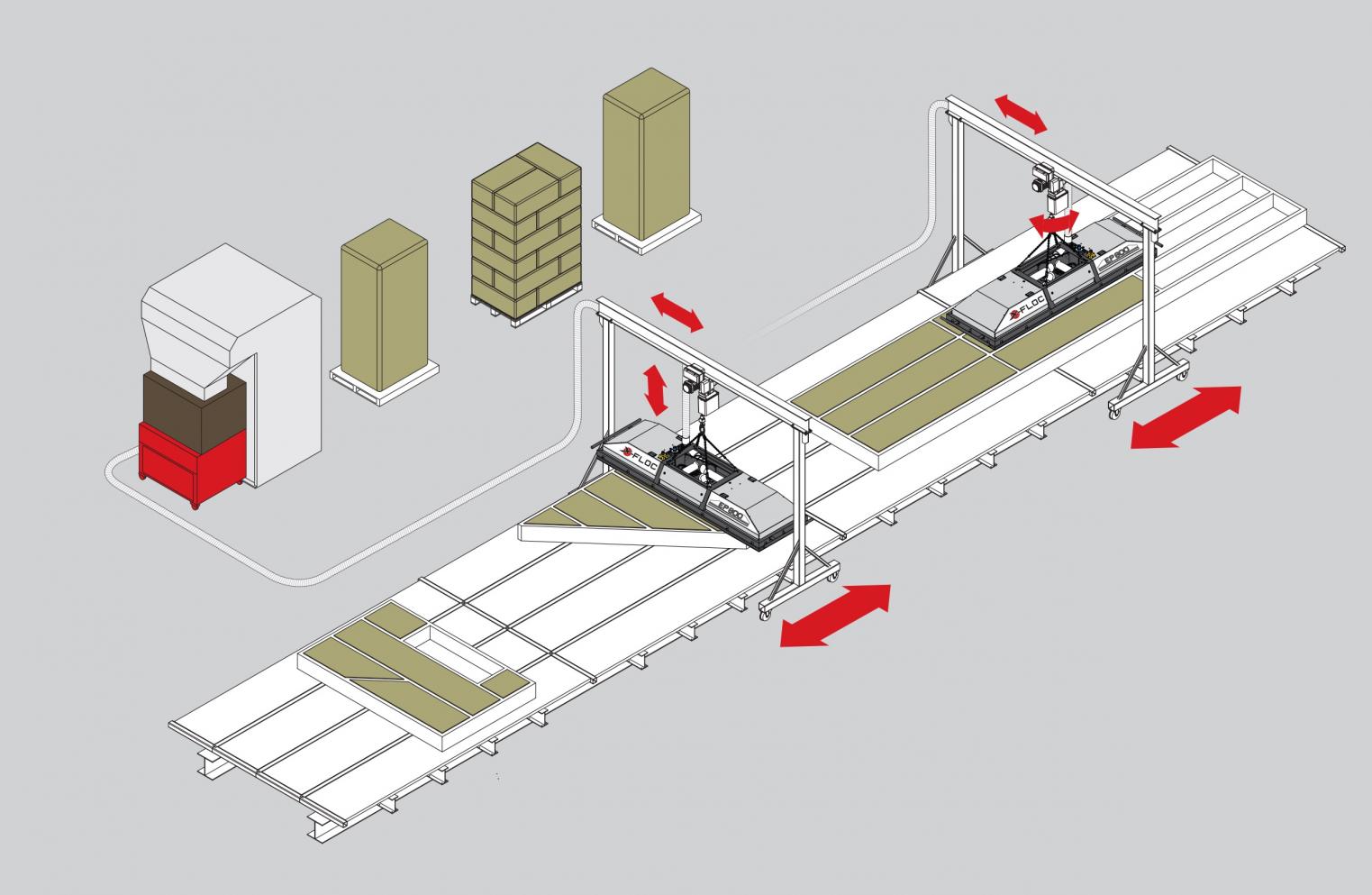
EM430 BLOW-IN MACHINE
Consistently high material throughput using tried and tested material shredders and powerful, durable turbine technology for air generation make the EM430 blowing machine the first choice for factory filling. The four rotating crusher shafts and two shredder shafts of the two-stage bulking machine prepare all loose insulating materials optimally for pneumatic conveying and professional fitting. The large rotary valve conveys the material loosened up in this way into the air flow of the five-stage high-performance turbine which provides the acceleration and transport required for the material.
The factory filling system’s controller can of course import all functions and parameters of the blowing machine that are responsible for a successful blowing process.
EP800 BLOWING PANEL
In the basic version, the EP800 blowing panel has five large injection nozzles and four pneumatically-driven material diverters (diameter = 3 inches), which enable material throughputs of up to 1,000 kg/h depending on the blown-in insulation used and the desired installation density. The injection nozzles can be adjusted in height by several centimetres to achieve an optimum injection pattern for each insulating material used. The material diverters can be supplied with the required compressed air in the factory itself or by an air compressor integrated into the blowing panel. A high-quality industrial control system “Made in Germany” and the software developed by x-floc control the EP800 blowing panel (and the other machines in a factory filling system). After positioning the blowing panel on the element which is open on one side, it is only necessary to enter the dimensions (length, width, height) and the insulating material used before the blowing process can be started. The program used in each case (with the blowing parameters individually set within it) and its signal evaluation of the connected measuring sensors ensure that the blowing panel or system is switched off at the right time. For archiving purposes and quality verification, all settings and results used during a blowing process (e.g. the mass of insulating material introduced into the element) are logged in detail.
The EP800 blowing panel seals off the element, which is open on one side, using a replaceable filter foam cover and its own weight to prevent the insulating material from escaping during the blowing process. The sturdy steel structure with sheet steel cladding provides the blowing panel with the necessary robustness to ensure the reliability required in daily use.
The blowing panel is operated via a wireless tablet computer for maximum flexibility. The five injection nozzles can be activated or deactivated individually, enabling expert filling of any element geometry.
GBF1050 BIG BALE CONDITIONER
The GBF1050 big bale conditioner ensures virtually uninterrupted filling of the blowing machine with the THERMOFLOC cellulose insulation. THERMOFLOC in the form of “big bales” is fed into the big bale conditioner using pallet trucks, forklifts or conveyor belts. The THERMOFLOC big bale is a compressed block of cellulose insulation manufactured in line with the requirements of the factory filling system.
The conditioning machine, consisting of 18 milling blades, removes the big bale layer by layer and conveys the cellulose material, which has already been loosened in this way, into the EM430 blowing machine combined with the big bale conditioner. The intelligent control system and using a large number of sensors on the big bale conditioner and blowing machine ensures a virtually uninterrupted supply of material.